Fireclay Refractories
Effective solution for operating in high-temperature conditions
Fireclay refractories are widely used in almost all common thermal units where high temperatures and operating conditions require materials to ensure reliability and long service life. Fireclay refractories rank first in refractory production, accounting for 65–70% of the total volume. Their widespread use is due to their availability and low cost, good thermal stability (up to 50 thermal cycles), and minimal shrinkage during firing. These unique materials, made from high-quality raw materials, guarantee the stability and safety of production processes in the metallurgy, cement, glass, and ceramics industries.
Types of Products
Taking into account the specific requirements of our customers, we offer the manufacturing and supply of refractory products in various shapes and configurations. Our advanced production capabilities and technological expertise enable us to handle projects of any complexity, ensuring high quality and precision in every delivery.
Technical Description
Our Fireclay refractories are manufactured from carefully selected refractory clay, fired at high temperatures to achieve optimal performance characteristics. Each production batch undergoes rigorous quality control to ensure compliance with
international standards.
- Heat Resistance and Thermal Stability – Fireclay refractories are renowned for their excellent thermal stability, withstanding temperatures of up to 1700°C. Their ability to endure prolonged exposure to high temperatures makes them ideal for applications requiring thermal endurance. Additionally, these materials exhibit outstanding thermal shock resistance, making them suitable for environments with abrupt temperature fluctuations.
- Strength and Durability – Fireclay refractories possess high mechanical strength and wear resistance, ensuring durability even in aggressive conditions. Their reliability significantly reduces replacement frequency and lowers maintenance costs.
- Format Flexibility – Fireclay refractories can be produced in a wide range of sizes and shapes, from standard bricks to
- custom-designed products tailored to meet the specific requirements of the customer’s equipment. This flexibility makes them ideal for a variety of industrial applications.
Erbau Industrial Group offers for delivery Fireclay refractory products, which according to DIN 1089 corresponds to the following quality indicators:
Table 1. Fireclay Type E
Properties | Е70 | Е65 | Tests in accordance with | |||||
Е70-1 | Е70-2 | Е65-1 | Е65-2 | |||||
Typical application | ||||||||
Oven overlap Flue ducts Regenerator Regenerators nozzle Lining | ||||||||
SiO2 | % | µG σ | ≥ 70 1,5 | ≥ 65 1,5 | DIN 51 062 DIN 51 070 Part 2 | |||
Apparent porosity (Ро) | % | µG σ | ≤ 23 1,5 | ≤ 21 1,5 | ≤ 25 1,5 | ≤ 22 1,5 | DIN 51 056 | |
Cold compressive strength | N/mm2 | µG σ Хmin | ≥ 25 10 15 | ≥ 40 20 20 | ≥ 20 10 15 | ≥ 35 15 20 | DIN 51 067 Part 1 | |
Refractoriness under load at initial temperature | °C | µG σ | ≥ 1,350 50 | ≥ 1,350 20 | ≥ 1,320 20 | DIN 51 064 | ||
Refractoriness under load (various methods) | °C | µG σ | By mutual agreement | DIN 51 053 Part 1 | ||||
Refractoriness | SK | µG σ | ≥ 158 (SK 26) 2 (SK 1) | – | DIN 51 063 Part 1 | |||
Compressive creep (DFI) | [Z5-25] | % | µG σ | ≤ 0.1 0,03 | DIN 51 053 Part 2 | |||
[Z25] | % | µG σ | ≤ 0,25 0.1 | |||||
Acid solubility (SL) | mm | µG σ | ≤ 5 | DIN 52 102 Part 2 | ||||
Thermal shock resistance (TWB) | Number of thermal cycles | By mutual agreement |
Table 2. Fireclay Type KA
Properties | КА 40 | КА 35 | Tests in accordance with | |||||
КА 40-1 | КА 40-2 | КА 35-1 | КА35-2 | |||||
Typical application | ||||||||
Oven headers Regenerators Regenerators nozzle | ………. Oven overlap | |||||||
Al2O3 | % | µG σ | ≥ 40 1,5 | ≥ 35 1,5 | DIN 51 070 Part 3 | |||
Fe2O3 | % | µG σ | ≤ 2.0 0,5 | ≤ 2.5 0,5 | DIN 51 070 Part 5 | |||
Apparent porosity (Ро) | % | µG σ | ≤ 20 2 | ≤ 24 2 | ≤ 19 2 | ≤ 24 2 | DIN 51 056 | |
Cold compressive strength | N/mm2 | µG σ Хmin | ≥ 35 10 25 | ≥ 30 10 20 | ≥ 30 10 20 | ≥ 30 10 20 | DIN 51 067 Part 1 | |
Refractoriness under load at initial temperature | °C | µG σ | ≥ 1,450 40 | ≥ 1,400 40 | ≥ 1,400 40 | ≥ 1,350 40 | ||
Refractoriness under load (various methods) | °C | µG σ | ≥ 1,350 25 | ≥ 1,300 25 | ≥ 1,300 25 | ≥ 1,250 25 | ||
Refractoriness | SK | µG σ | ≥ 172/174 (SK 33) 2 (SK 1) | – – | DIN 51 063 Part 1 | |||
Compressive creep (DFI) | [Z5-25] | % | µG σ | ≤ 0,1 0,03 | DIN 51 053 Part 2 | |||
[Z25] | % | µG σ | ≤ 0,25 0,1 | |||||
Thermal shock resistance (TWB) | Number of thermal cycles | By mutual agreement |
To receive the best service and quality
How the Production Process Works
Production of Fireclay refractories includes several key stages that enable the creation of products with high refractory properties, mechanical strength, and durability. The main stages of the process are described below:
Raw Material Preparation
The raw materials for the production of Fireclay products consist of a mixture of chamotte (calcined clay) and refractory clays or kaolins. The presence of chamotte in the batch reduces shrinkage and cracking of the product during heating at temperatures of 1300–1400°C.
Crushing: After firing, chamotte undergoes coarse crushing followed by fine grinding. The ground chamotte is then sieved and divided into fractions based on grain size. Refractory clay preparation involves removing mechanical impurities and drying in rotary dryers. The dried clay is then ground in ball mills. Raw materials are crushed to the required grain size, which depends on the final purpose of the product.
Additives: During the production process, clay materials are added as plastic binding components, along with organic additives to improve forming.
Product Forming
Mixing: Crushed components are thoroughly mixed to ensure the uniform distribution of the coarse (chamotte) and binding (clay) materials, even moisture distribution, and the creation of a homogeneous mixture.
Forming: Mixture is pressed into molds to create blanks such as bricks, blocks, or other shaped products. This process can be carried out using hydraulic or mechanical presses under high pressure to ensure the required density of the semi-finished product, which is essential for meeting the standard specifications of the final products. The molds are designed for both standard sizes and complex configurations, including custom designs based on customer specifications.
Drying
Sufficient mechanical strength and density of the semi-finished product allow for direct drying in tunnel kilns on kiln cars. The first zone of the kiln serves as a dryer, where moisture is reduced to 2–3%.
Slow drying is used for products manufactured by plastic pressing. The blanks are dried at low temperatures (50–120°C) in special drying chambers or tunnels. This process ensures moisture removal without causing cracks in the products.
Moisture Control: Moisture content of the products is gradually reduced to 3–5%, leading to a decrease in linear dimensions (shrinkage). This step is essential to prepare the products for firing.
Firing products
High-Temperature Firing: Blanks are fired in tunnel kilns at temperatures ranging from 1350 to 1500°C. During the firing process, clay minerals undergo dehydration, and bonds form between the raw material components. Chamotte becomes structurally stable, providing high thermal resistance and mechanical strength.
Cooling: After firing, the products are cooled under controlled conditions to avoid internal stresses and defects.
Quality Control
Parameter Testing: Finished products are inspected to ensure they meet quality standards for parameters such as refractoriness, compressive strength, porosity, and chemical resistance.
Sample Testing: Samples are taken from each batch. The selected samples undergo laboratory testing to assess their quality.
Packaging and Transportation
Finished products are packaged to protect them from mechanical damage and environmental exposure during transportation.

Historical Background of Fireclay Refractories
The term “chamotte” originates from the French word chamotte, which, in turn, comes from the name of a region in France known for its deposits of special clay used in the production of refractory materials. Historically, chamotte gained popularity due to its ability to withstand extreme temperatures. By the Middle Ages, it was actively utilized in metallurgy and kilns for firing ceramics.
Mass production of chamotte (fireclay) in its modern form began in the early 19th century, following the development of technologies that allowed for firing specific clays at high temperatures to achieve the desired thermal and mechanical properties. During this period, chamotte (fireclay) was widely used in the metallurgical industry, particularly for the production of furnace linings.
By the mid-20th century, chamotte (fireclay) materials became a key component in the production of refractory bricks for blast furnaces, pipelines, as well as insulation and lining materials for various industrial installations requiring high thermal resistance. Modern chamotte (fireclay) production methods enable the creation of materials capable of withstanding temperatures above 1500°C – 1580°C, with excellent chemical resistance to aggressive environments.
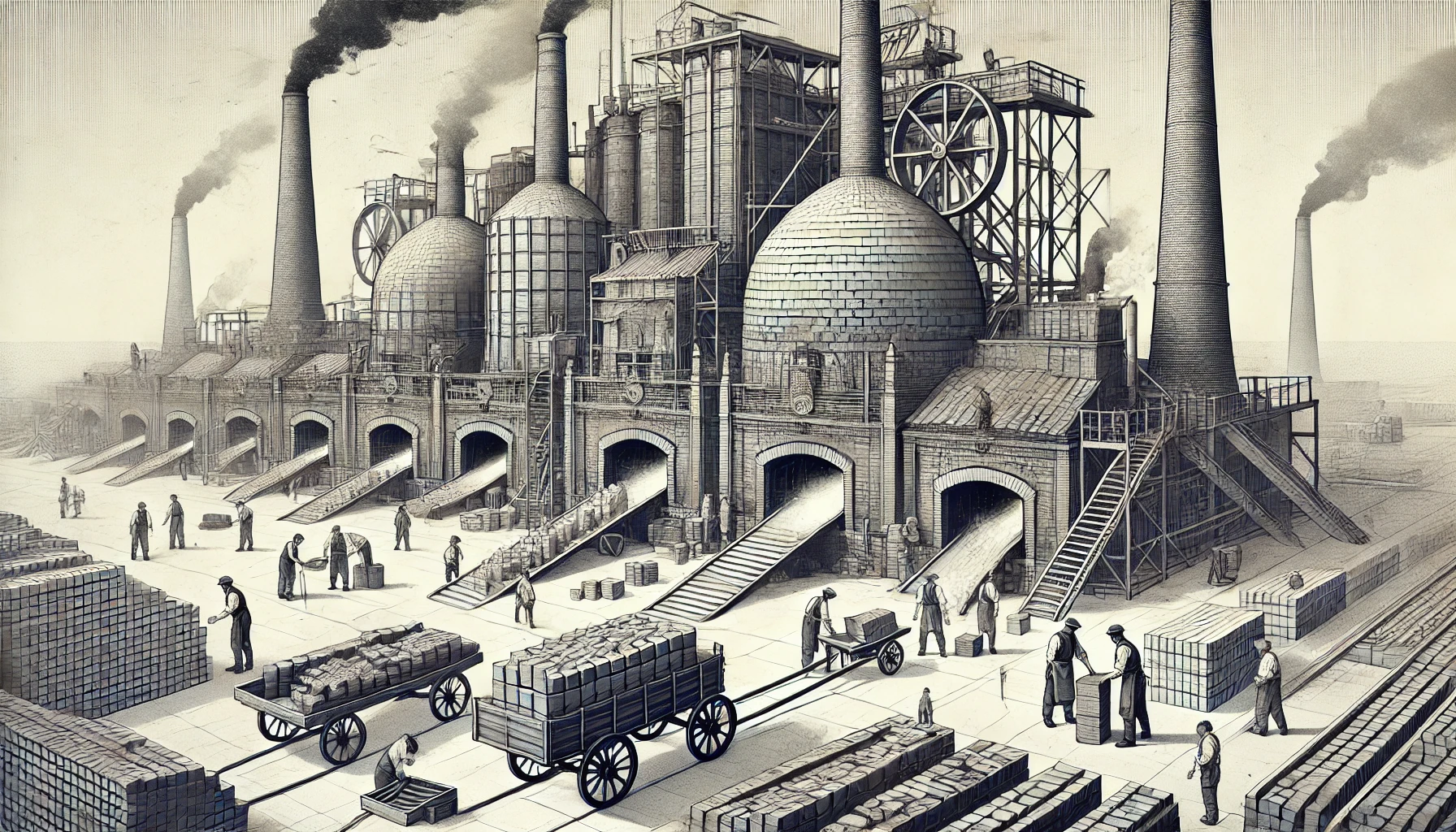